Continuous Improvement: Definition & The 6 Stages

Navigating Continuous Improvement: Key Strategies for Sustainable Success
With Wayne's rich background in driving successful business operations, this article explores the critical stages of continuous improvement that are essential for any organization aiming to stay competitive and achieve sustained growth.
Understanding Continuous Improvement
Comprehending the concept of Continuous Improvement is essential for organizations striving to enhance their processes and achieve sustainable growth. This involves a methodical approach to refining operations through the implementation of methodologies such as Lean, Kanban, Six Sigma, Total Quality Management, and Agile practices.
Continuous improvement cultivates a culture of innovation and efficiency within businesses. By consistently seeking opportunities to optimize workflows and eliminate inefficiencies, organizations can maintain competitiveness in dynamic markets.
The Lean methodology concentrates on minimizing waste and maximizing value creation, while Kanban aids in visualizing workflows to enhance efficiency. Six Sigma places emphasis on statistical methods to reduce defects, and Total Quality Management aims for continual quality enhancement.
Agile Methodology promotes flexibility and adaptability in project management, enabling teams to promptly respond to shifting requirements.
Definition and Importance
Continuous improvement refers to the ongoing initiative aimed at enhancing processes, products, or services within an organization to bolster efficiency and effectiveness. It embodies a culture rooted in perpetual refinement and innovation, with guidance often drawn from methodologies such as Lean, Kanban, Six Sigma, Total Quality Management, and Agile practices.
These methodologies offer structured frameworks that organizations can implement to pinpoint areas in need of enhancement, streamline operations, and enhance quality standards. The Lean methodology is centered on the removal of waste and optimization of processes, while Kanban visualizes workflows to facilitate improved task management.
Six Sigma strives to reduce defects and variations in processes, ensuring consistent outcomes. Total Quality Management underscores a customer-centric approach to provide superior products or services. Agile Methodology emphasizes adaptability and collaboration to enable swift responses to evolving market demands.
The 6 Stages of Continuous Improvement
The 6 Stages of Continuous Improvement provide a structured approach aimed at driving organizational advancement through iterative processes. These stages typically adhere to the principles of Lean Continuous Improvement (LCI) and the Plan-Do-Check-Act cycle to ensure effective implementation and sustainability.
Commencing with the initial stage, the emphasis lies on recognizing the necessity for change and establishing specific improvement objectives. This stage correlates with the 'Plan' phase within the PDCA cycle, during which a comprehensive plan is developed.
Progressing to the second stage, actions are executed in accordance with the established plan, reflecting the 'Do' phase of the cycle. The third stage involves assessing the outcomes and comparing them to the predetermined goals, similar to the 'Check' phase.
Following this, the fourth stage entails making adjustments to optimize processes and improve outcomes, aligning with the 'Act' phase. Each stage underscores the significance of engaging employees, soliciting feedback, and consistently refining strategies to cultivate sustainable enhancements.
Stage 1: Identifying Areas for Improvement
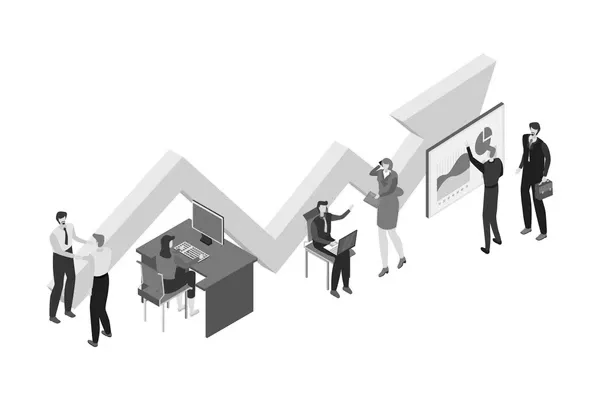
During the initial phase of continuous improvement, organizations concentrate on pinpointing areas for enhancement through the utilization of employee insights, analysis of pertinent data, and alignment of strategies with the tenets of Lean Continuous Improvement.
The process of identifying areas for improvement is of paramount importance as it allows organizations to effectively prioritize their initiatives. By engaging employees in this process, companies can leverage their frontline experience and unique perspectives, thereby transforming them into active agents of change. Data analysis assumes a critical role in this phase, enabling organizations to identify specific areas requiring improvement and monitor progress over time. Aligning strategies with Lean Continuous Improvement principles ensures that enhancements are executed in a systematic and sustainable manner, fostering a culture of continuous learning and advancement within the organization.
Stage 2: Setting Goals and Objectives
In the second phase of continuous improvement, organizations establish clear goals and objectives designed to enhance efficiency and align with the principles of the Lean Method. This stage frequently involves the implementation of the Plan-Do-Check-Act cycle to ensure the achievement of these goals.
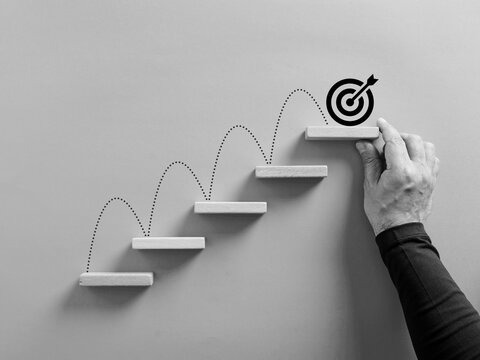
By defining specific and measurable targets, teams can concentrate their efforts on areas that necessitate improvement, thereby promoting organizational alignment and optimizing processes. Continuous improvement endeavors hinge on the delineation of SMART objectives — those that are specific, measurable, achievable, relevant, and time-bound. Teams utilize data and performance metrics to evaluate progress and make data-driven decisions to further enhance efficiency. The cyclical nature of the PDCA cycle ensures that adaptations are made as required, fostering a culture of continuous learning and development within the organization.
Stage 3: Developing Action Plans
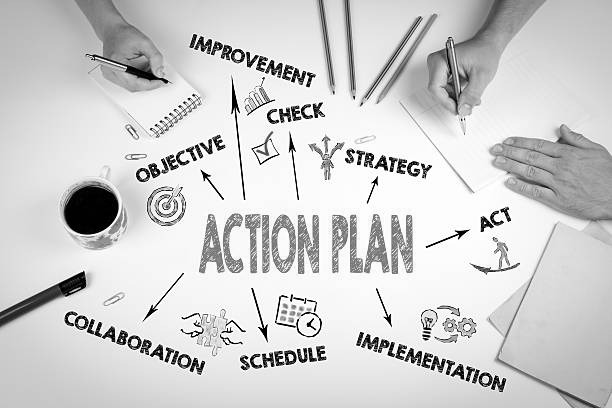
During the third stage, organizations formulate detailed action plans to translate goals into tangible outcomes. This phase typically involves implementing strategies rooted in Lean and Kanban methodologies while actively involving employees in the execution process.
The Lean methodology, which emphasizes the elimination of wasteful processes, plays a pivotal role in refining action steps to enhance efficiency. Concurrently, the Kanban methodology assists in visualizing workflows and ensuring the smooth progression of tasks through each stage.
Employee engagement is paramount during this phase, as their insights can augment the efficacy of the plans and cultivate a sense of ownership. By actively engaging team members in the execution process, organizations can stimulate motivation, foster innovation, and promote continuous improvement throughout the implementation phase.