Techniques for Improving Business Process Efficiency: 7 Best Practices
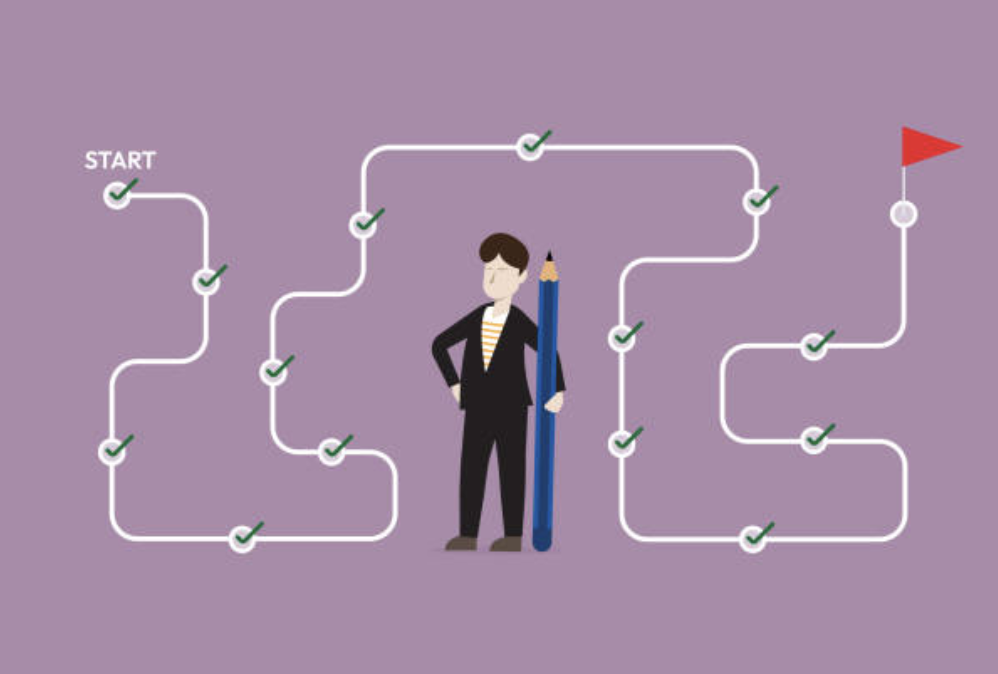
Unlock the secrets to higher productivity with these 7 best practices for improving business process efficiency.
As a seasoned entrepreneur featured on Entrepreneur.com and expert in streamlining operations, I've developed practical techniques for boosting efficiency.
This article details seven best practices to refine your processes, ensuring your business operates at peak performance.
Before diving into the 7 practices, let's learn the basics of business process!
The Importance of Business Process Efficiency
The efficiency of business processes is paramount for any organization seeking success, as it directly influences employee performance, the quality of products or services, and the overall operational excellence of the enterprise.
Effective processes guarantee that an organization can uphold superior standards of quality management while maximizing resource utilization and reducing waste.
Why Efficiency Matters in Business Processes
Efficiency in business processes is a critical element as it serves to enhance overall performance, minimize costs, and elevate the quality of outputs.
When processes demonstrate efficiency, organizations can allocate resources with greater precision, leverage advanced tools, and sustain competitive advantages within their respective markets.
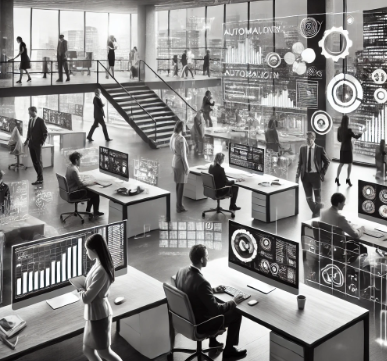
Efficiency plays a pivotal role in the facilitation of streamlined workflows, waste reduction, and the promotion of timely decision-making.
Through the utilization of tools such as automation software, data analytics, and workflow management systems, businesses can refine their operations and enhance productivity.
Efficient processes not only assist in promptly meeting customer demands but also set the stage for continual improvement and innovation.
The integration of technology and adherence to best practices are essential components in nurturing efficiency and fostering sustainable growth within the dynamic landscape of modern business environments.
Identifying Inefficient Processes
The initial phase in effectuating substantive enhancements within an organization involves the identification of inefficient processes.
It is imperative for business leaders and project teams to undertake comprehensive analyses and workflow assessments in order to accurately identify areas necessitating modifications and improvements.
Signs to Look For
Indications of ineffective processes commonly manifest as frequent bottlenecks, repetitive tasks, and unsatisfactory performance evaluations.
These signs serve as alerts that certain areas necessitate immediate attention to elevate overall operational efficiency.
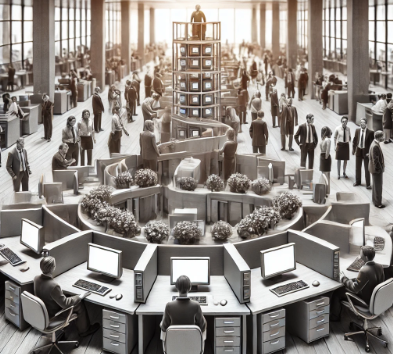
Bottlenecks within a process have the potential to create delays and disrupt the entire workflow, consequently diminishing productivity levels.
The presence of repetitive tasks not only consumes valuable time but also signals opportunities for automation or process streamlining.
Additionally, receiving poor performance reviews frequently underscores the areas where employees encounter difficulties as a result of inefficient processes. Such challenges can significantly impact the organization's overall performance.
By attentively observing these indicators, organizations can pinpoint specific problem areas and enact precise enhancements to optimize their processes, thereby yielding superior outcomes.
Best Practices for Improving Business Process Efficiency
The implementation of optimal practices to enhance business process efficiency encompasses the adoption of established strategies such as Kaizen, Six Sigma, Lean Manufacturing, and Agile methodology.
These methodologies offer a structured framework for ongoing enhancement and assist organizations in attaining elevated levels of efficiency.
1. Streamlining and Standardizing Processes
The optimization and standardization of processes are crucial steps in improving business efficiency and ensuring a consistent level of quality.
The principles of Total Quality Management (TQM) can be effectively utilized to establish standardized workflows that minimize variability and enhance overall process efficacy.
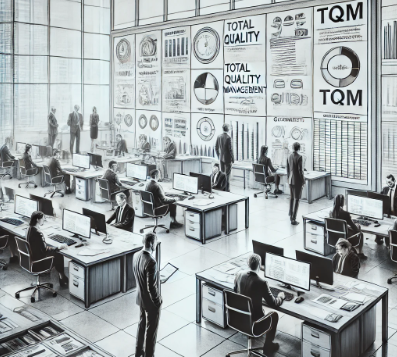
Through the integration of TQM principles, organizations can define explicit guidelines and procedures that clarify the roles and responsibilities of employees within the workflow.
Standardizing processes not only boosts efficiency but also promotes better communication and collaboration among various departments.
This standardization contributes to heightened customer satisfaction, as products or services are consistently delivered to meet or surpass expectations.
The implementation of standardized workflows facilitates the identification of bottlenecks or areas in need of enhancement, thus enabling the continual improvement of operational efficiency.
2. Automating Repetitive Tasks
The automation of repetitive tasks yields significant benefits by optimizing efficiency and enabling employees to allocate their time towards more strategic endeavors.
Platforms such as ClickUp present opportunities to automate various mundane tasks, resulting in heightened productivity levels and a reduction in errors.
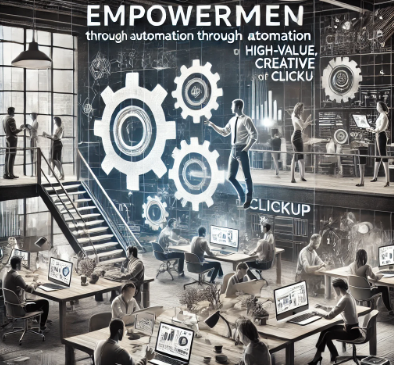
This automation liberates employees from the burden of monotonous duties, allowing them to redirect their attention towards high-value initiatives that demand critical thinking and creativity.
By streamlining operations through tools like ClickUp, organizations can witness an enhancement in overall performance and output.
Through the delegation of repetitive tasks such as data entry, scheduling, and reminders to automation, employees are afforded the opportunity to concentrate on innovation and complex problem-solving.
This not only amplifies productivity but also diminishes the likelihood of human errors, ensuring a more precise and effective workflow.
3. Regularly Reviewing and Updating Processes
Regularly reviewing and updating processes is essential for sustaining optimal performance and adapting to shifts in the business landscape.
Continuous analysis plays a pivotal role in pinpointing areas for enhancement and executing requisite modifications to maintain competitiveness.
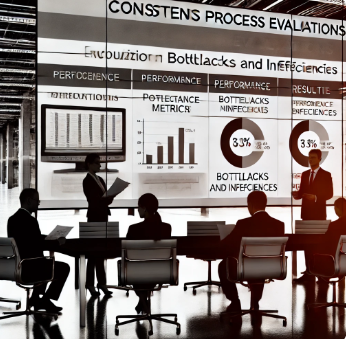
Through consistent process evaluations, organizations can ascertain that their operations are running with utmost efficiency and efficacy.
Performance analysis not only offers insights into present performance benchmarks but also illuminates any bottlenecks or inefficiencies that might impede progress.
This data give the power to businesses to make well-informed decisions regarding the necessary alterations to boost productivity and overall efficacy.
In the current dynamic markets, the capacity to adapt swiftly is imperative for outpacing competitors and addressing the evolving demands of customers.